Solid Silicone vs. Liquid Silicone Rubber (LSR) – OEM Material Comparison Guide
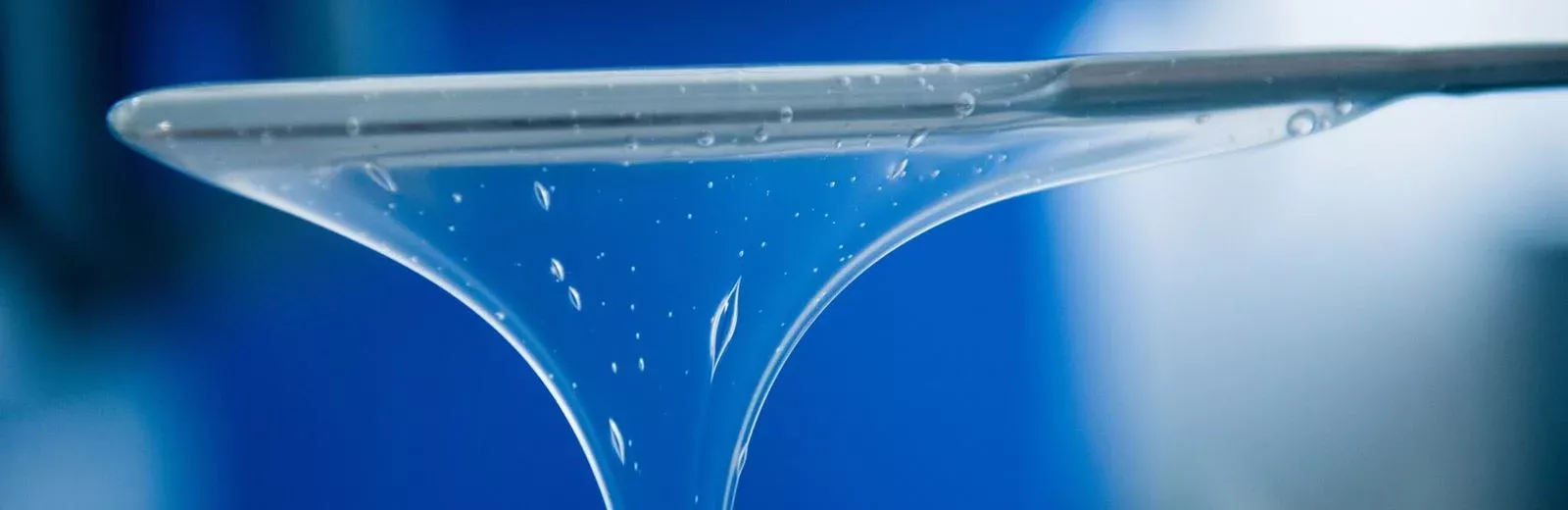
Solid vs. Liquid Silicone Rubber: Which One Should You Use for OEM Production?
When planning a custom silicone product, selecting the right material is one of the most critical decisions. The two most commonly used types in silicone OEM manufacturing are Solid Silicone Rubber (HTV) and Liquid Silicone Rubber (LSR). Though both are high-purity silicones, they differ significantly in processing, performance, and cost.
This article offers an in-depth comparison of solid vs. liquid silicone rubber — helping you decide which is more suitable for your project.
H2: What Is Solid Silicone Rubber?
Solid silicone rubber, often referred to as HTV (High-Temperature Vulcanizing silicone), is a silicone compound supplied in block or sheet form. It is typically cured using compression molding or transfer molding and requires external heat and pressure for vulcanization.
Characteristics:
-
Comes in a putty-like, solid form
-
Requires heat and pressure to cure
-
Can be post-cured for enhanced performance
-
Available in a wide range of hardness (Shore A)
Best Used For:
-
Keypads
-
Gaskets
-
Seals
-
Silicone kitchenware
-
Automotive components
H2: What Is Liquid Silicone Rubber (LSR)?
Liquid Silicone Rubber is a two-part platinum-cured system with a low viscosity that allows it to be injection molded. This makes LSR ideal for high-volume production with complex geometries and tight tolerances.
Characteristics:
-
Low viscosity, flows easily into molds
-
Highly automated, suitable for precision parts
-
Fast curing at elevated temperatures
-
Excellent transparency and biocompatibility
Best Used For:
-
Baby products (pacifiers, nipples)
-
Medical devices
-
Wearables
-
Electrical connectors
-
Micro components
H2: Processing Comparison
Feature | Solid Silicone Rubber (HTV) | Liquid Silicone Rubber (LSR) |
---|---|---|
Processing Method | Compression / Transfer Molding | Liquid Injection Molding (LIM) |
Mold Cost | Lower | Higher |
Cycle Time | Longer | Faster |
Tolerances | Moderate | Tight |
Automation | Manual or Semi-Auto | Fully Automated |
Material Cost | Lower | Higher |
H2: Performance Comparison
-
Thermal Stability: Both offer excellent high and low-temperature resistance (-60°C to 230°C).
-
Tear Strength: LSR generally offers better tear strength and elasticity.
-
Transparency: LSR is preferred for translucent or colored products.
-
Biocompatibility: LSR is often FDA, USP Class VI, and ISO 10993 compliant.
H2: Pros and Cons Summary
Solid Silicone Rubber (HTV)
✅ Pros:
-
Lower tooling costs
-
Good for low-to-medium volume
-
Suitable for thick parts
❌ Cons:
-
Manual handling increases labor
-
Slower production cycle
-
Less precise for micro parts
Liquid Silicone Rubber (LSR)
✅ Pros:
-
Excellent for high-volume production
-
Great consistency and repeatability
-
High biocompatibility
❌ Cons:
-
Higher upfront mold cost
-
Requires precision equipment
-
Not ideal for simple or thick-walled parts
H2: How to Choose the Right Material for Your Silicone OEM Project?
Ask the following:
-
Is your design complex or micro-sized?
-
Do you require FDA or medical-grade approval?
-
What’s your expected production volume?
-
Are tight tolerances essential?
-
What’s your budget for tooling?
If you're not sure, we can help analyze your drawings and recommend the best fit.
H2: Final Thoughts
Both solid and liquid silicone rubber have important roles in silicone manufacturing. The right choice depends on your product design, performance needs, and production scale.
At our silicone OEM factory, we specialize in both HTV and LSR processing. Whether you're looking for low-cost prototyping or scalable production with automated molding, we offer tailored solutions based on your unique needs.
📌 Internal Linking Suggestions:
-
Link to your Services Page under “OEM silicone molding”
-
Link to a Product Page if showcasing LSR items
-
Link to a Contact Page with CTA like “Need help choosing materials? Contact our team”
Would you like me to move on to Post 2: “5 Things to Know Before Customizing a Silicone Mold” next?